www.technologieenindustrie.com
28
'10
Written on Modified on
NZ Steel doet beroep op Verlinde
KraneQuip, verdeler van Verlinde in Nieuw-Zeeland, stond voor de uitdaging om een rationele oplossing te zoeken voor de creatie en constructie van een loopkraan met een capaciteit van 16 ton, bestemd voor een heel beperkte ruimte bij NZ Steel.
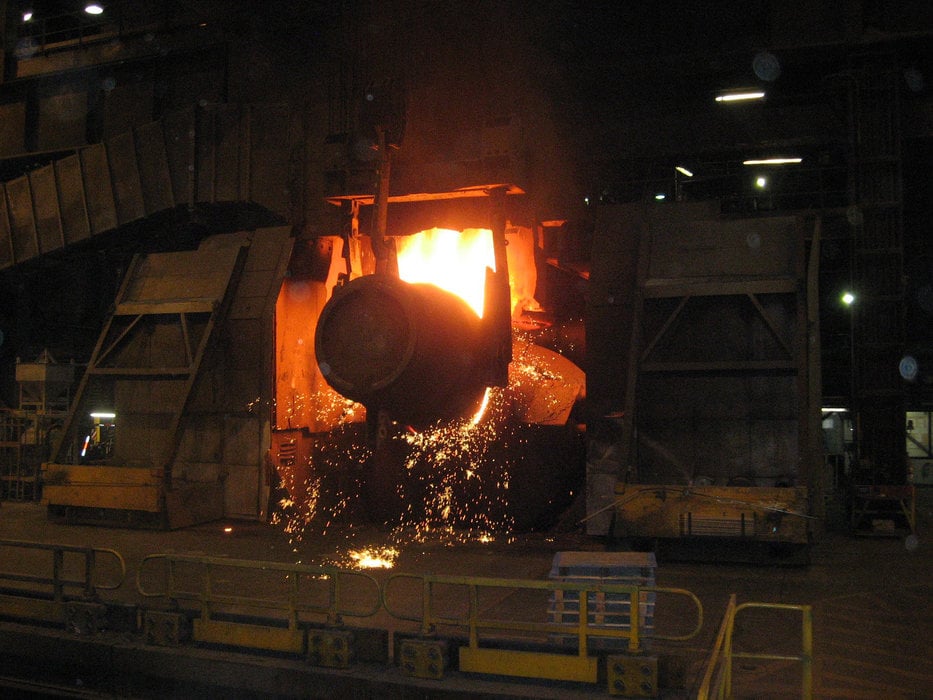
In september 2008 werd KraneQuip aangesproken door NZ Steel voor de implementatie van een loopkraan met een capaciteit van 16 ton, bestemd voor de vervanging van de gasemissieleidingen in haar staalplaat fabriek. « Dit was allesbehalve een standaard ontwerp. Door een aantal beperkingen en voorwaarden kreeg dit verzoek een heel bijzonder karakter", aldus de ingenieur Cobus van der Walt van KraneQuip.
Het eerste probleem was de ruimte waarin de rolbrug zou moeten passen. « Het was een enorme uitdaging om deze te plaatsen in een ruimte van vier meter breed. Vooral met een hijshoogte van 30 meter, bekent Cobus Van der Walt. Daarvoor heeft men normaal gezien een staaldraadtakel nodig, maar met een takeltrommel die groot genoeg is voor het oprollen van 30 meter kabel. Dit betekent dat de trommel bijna zo groot als de beschikbare ruimte zou moeten zijn ». De puntbelasting moest van oost naar west worden verplaatst over de balk van de rolbrug, maar een staaldraadtakel was niet mogelijk wegens de grootte. « Toen hebben we de kettingtakels bestudeerd. Maar het probleem met kettinglieren is dat er geen bestaan van meer dan vijf ton, of in ons geval 7,5 ton, want onze leverancier, Verlinde, kon er één fabriceren met deze capaciteit. Toch waren we nog ver van de benodigde 16 ton ». Na veel nadenken, heeft het team KraneQuip voorgesteld om twee kettingtakels te gebruiken met elk een capaciteit van tien ton. In de praktijk dienden echter twee kabels van vijf ton aan elkaar te worden gekoppeld om 10 ton per assemblage te bereiken. Vervolgens dienden twee van deze assemblages op de balk van de rolbrug te worden geplaatst.
«Dankzij de sterke ontwerpcapaciteiten konden we reeds een paar weken later de lieren installeren op een balk van de monorail rolbrug, waarbij aan de vereiste grootte van de te verplaatsen puntbelasting werd voldaan. Daarvoor dienden we de afmetingen van de hoekbalken te wijzigen met slechts enkele millimeters».
De volgende uitdaging bestond erin een rolbrug te bouwen die 16 ton kon dragen. De sterkste rechte standaardbalk was niet voldoende en een kokerligger zou te duur zijn. KraneQuip moest daarom een rechte brugbalk met bovenversterking en onderflenzen ontwerpen om de last te kunnen dragen. Dankzij deze oplossing heeft het team de levertijd kunnen verkorten en NZ Steel extra kosten bespaard die met de fabricatie van een kokerligger zouden ontstaan zijn.
De buitenafmetingen van de kettingkasten vormden een bijkomend probleem. De twee takelassemblages, hoewel perfect aangepast aan het ontwerp, konden niet dicht genoeg bij elkaar komen om te voldoen aan de vereiste afstand ten opzichte van oost en west. Daarom dienden de twee centrale kettingkasten te worden gewijzigd. « We konden niet nog dieper dalen, omdat er geen plaats meer was. Bijgevolg hebben we in de breedte gewerkt», aldus Cobus van der Walt. Dit zorgde echter voor een ander probleem: de ketting moest de volledige breedte van de kasten vullen. Het team heeft dus deflectorplaten in het midden geplaatst en de hals van de kast geopend zodat de ketting zich binnen de kast zo goed mogelijk kon verspreiden. De eerste realisatie werkte niet, maar na enkele wijzigingen was het gelukt.
Bij de inbedrijfstelling, was het noodzakelijk verschillende afstellingen uit te voeren om een identieke translatiebeweging van beide haken op dezelfde hoogte te verzekeren evenals de gelijktijdige activering van de hoekbalkschakelaars. Talloze problemen ontstonden met de verplaatsingssnelheid in de lengte, omdat de kraan zich in alle richtingen slechts heel traag kon bewegen. Er werd een variabele snelheidsregeling gebruikt om de bediening vlot te doen verlopen. Met deze verplaatsing in de lengte, hoopte zich echter het vuil op in de rails en de wielen bleken te breed om de last van de hele kraan en de maximale veilige werklast te dragen. Het vermogen bij lage snelheid was nauwelijks voldoende om de kraan te doen bewegen en het vuil heeft enkele blokkeringen teweeggebracht. Uiteindelijk werd besloten dat de enige oplossing erin bestond al het vuil volledig uit de rails te verwijderen vóór elk gebruik.
« Dit project was voor het KraneQuip team een ongekende uitdaging en we zijn trots op de verwezenlijking ervan”, aldus Cobus van der Walt. Het is fantastisch de gelegenheid te hebben gehad om aan de zeer specifieke eisen van NZ Steel te voldoen, zelfs indien dit soms onmogelijk leek! ».
Het eerste probleem was de ruimte waarin de rolbrug zou moeten passen. « Het was een enorme uitdaging om deze te plaatsen in een ruimte van vier meter breed. Vooral met een hijshoogte van 30 meter, bekent Cobus Van der Walt. Daarvoor heeft men normaal gezien een staaldraadtakel nodig, maar met een takeltrommel die groot genoeg is voor het oprollen van 30 meter kabel. Dit betekent dat de trommel bijna zo groot als de beschikbare ruimte zou moeten zijn ». De puntbelasting moest van oost naar west worden verplaatst over de balk van de rolbrug, maar een staaldraadtakel was niet mogelijk wegens de grootte. « Toen hebben we de kettingtakels bestudeerd. Maar het probleem met kettinglieren is dat er geen bestaan van meer dan vijf ton, of in ons geval 7,5 ton, want onze leverancier, Verlinde, kon er één fabriceren met deze capaciteit. Toch waren we nog ver van de benodigde 16 ton ». Na veel nadenken, heeft het team KraneQuip voorgesteld om twee kettingtakels te gebruiken met elk een capaciteit van tien ton. In de praktijk dienden echter twee kabels van vijf ton aan elkaar te worden gekoppeld om 10 ton per assemblage te bereiken. Vervolgens dienden twee van deze assemblages op de balk van de rolbrug te worden geplaatst.
«Dankzij de sterke ontwerpcapaciteiten konden we reeds een paar weken later de lieren installeren op een balk van de monorail rolbrug, waarbij aan de vereiste grootte van de te verplaatsen puntbelasting werd voldaan. Daarvoor dienden we de afmetingen van de hoekbalken te wijzigen met slechts enkele millimeters».
De volgende uitdaging bestond erin een rolbrug te bouwen die 16 ton kon dragen. De sterkste rechte standaardbalk was niet voldoende en een kokerligger zou te duur zijn. KraneQuip moest daarom een rechte brugbalk met bovenversterking en onderflenzen ontwerpen om de last te kunnen dragen. Dankzij deze oplossing heeft het team de levertijd kunnen verkorten en NZ Steel extra kosten bespaard die met de fabricatie van een kokerligger zouden ontstaan zijn.
De buitenafmetingen van de kettingkasten vormden een bijkomend probleem. De twee takelassemblages, hoewel perfect aangepast aan het ontwerp, konden niet dicht genoeg bij elkaar komen om te voldoen aan de vereiste afstand ten opzichte van oost en west. Daarom dienden de twee centrale kettingkasten te worden gewijzigd. « We konden niet nog dieper dalen, omdat er geen plaats meer was. Bijgevolg hebben we in de breedte gewerkt», aldus Cobus van der Walt. Dit zorgde echter voor een ander probleem: de ketting moest de volledige breedte van de kasten vullen. Het team heeft dus deflectorplaten in het midden geplaatst en de hals van de kast geopend zodat de ketting zich binnen de kast zo goed mogelijk kon verspreiden. De eerste realisatie werkte niet, maar na enkele wijzigingen was het gelukt.
Bij de inbedrijfstelling, was het noodzakelijk verschillende afstellingen uit te voeren om een identieke translatiebeweging van beide haken op dezelfde hoogte te verzekeren evenals de gelijktijdige activering van de hoekbalkschakelaars. Talloze problemen ontstonden met de verplaatsingssnelheid in de lengte, omdat de kraan zich in alle richtingen slechts heel traag kon bewegen. Er werd een variabele snelheidsregeling gebruikt om de bediening vlot te doen verlopen. Met deze verplaatsing in de lengte, hoopte zich echter het vuil op in de rails en de wielen bleken te breed om de last van de hele kraan en de maximale veilige werklast te dragen. Het vermogen bij lage snelheid was nauwelijks voldoende om de kraan te doen bewegen en het vuil heeft enkele blokkeringen teweeggebracht. Uiteindelijk werd besloten dat de enige oplossing erin bestond al het vuil volledig uit de rails te verwijderen vóór elk gebruik.
« Dit project was voor het KraneQuip team een ongekende uitdaging en we zijn trots op de verwezenlijking ervan”, aldus Cobus van der Walt. Het is fantastisch de gelegenheid te hebben gehad om aan de zeer specifieke eisen van NZ Steel te voldoen, zelfs indien dit soms onmogelijk leek! ».