www.technologieenindustrie.com
17
'22
Written on Modified on
5 MANIEREN WAAROP DIGITAL TWINS OEM’S VAN WAARDE ZIJN IN DE HELE LEVENSCYCLUS VAN MACHINES
Door de veranderende eisen van klanten zijn traditionele processen voor het ontwerpen en bouwen van machines verouderd. Eindgebruikers verwachten volledig in bedrijf gestelde, productieklare slimme machines die sneller en betrouwbaarder presteren.
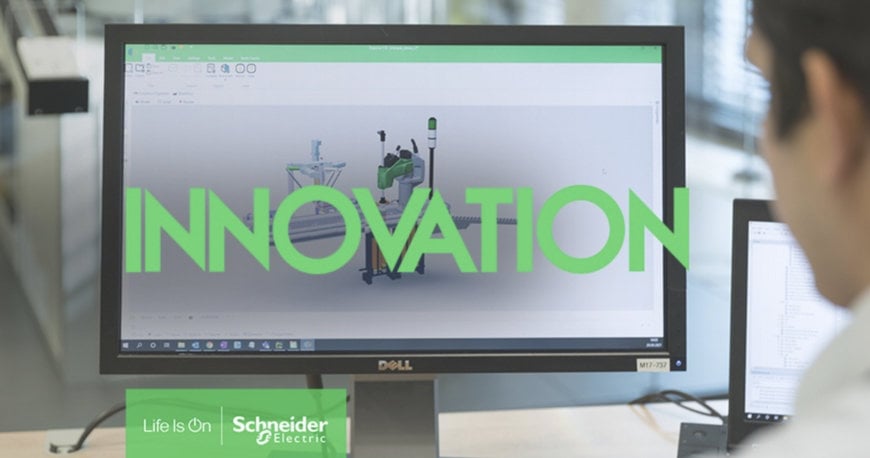
Een digital twin is een virtueel model dat OEM's kunnen gebruiken om:
- De besturingslogica te testen via gedetailleerde grafieken, waarbij het systeem virtueel in bedrijf wordt gesteld, met of zonder de hardware.
- De kans op ontwerpfouten te minimaliseren en het machinebouwproces te stroomlijnen.
- Aan te geven waar efficiëntieverbeteringen mogelijk zijn en hoe storingen te voorkomen.
- De virtuele en fysieke werelden (de twin) te koppelen, data-analyse en monitoringsystemen om proactief problemen te helpen voorkomen voordat ze zich voordoen.
- Het grote voordeel van digital twins ten opzichte van meer traditionele tools zoals CAD is de mogelijkheid om de impact van wijzigingen aan het machineontwerp te simuleren en te documenteren zonder te hoeven investeren in het bouwen van fysieke prototypes.
Digital twins bieden voordelen voor de hele levenscyclus van machines
Nieuwe 3D digital twin-tools, zoals EcoStruxure Machine Expert Twin-platform van Schneider Electric, bieden waarde aan de interacties tussen OEM en eindklant in alle belangrijke fasen van de levenscyclus van machines:
1. Meer verkoop van machines
De 3D-animaties laten potentiële klanten in duidelijk detail zien hoe hun machines eruit zullen zien en hoe ze zullen werken voordat de machine is gebouwd. Dit krachtige hulpmiddel wekt de interesse van de klant en schept realistische gedeelde verwachtingen. Digitale "proof of concept"-activiteiten maken interactie met potentiële klanten en vroege validatie van machineontwerpconcepten mogelijk.
2. Betrouwbaarder machineontwerp
Het gebruik van kant-en-klare programmeerobjecten maakt het voor engineers eenvoudiger om een consistente machinekwaliteit te realiseren en biedt de flexibiliteit om ontwerpideeën eenvoudig te wijzigen en te valideren, zelfs voor zeer complexe automatiseringssystemen. Tijdens de O&O-ontwerp- en machineontwikkelingsfasen maakt virtual engineering gedifferentieerde, snelle machineontwerpen mogelijk met een verbetering van de ontwerpkwaliteit tot 30%.
3. Snellere machinebouw
De digital twin importeert eenvoudig data uit meerdere bronnen, zoals AutoCAD-systemen, Excel-spreadsheets, XML en vooraf gebouwde sjablonen uit eerdere projecten. Dankzij de multidimensionale database van de software is het niet meer nodig om honderden kopieën te maken binnen hetzelfde project. Het maakt grafische voorstellingen, statusconfiguraties, revisie datalagen en operationele parameters binnen hetzelfde projectbestand mogelijk. Referentieontwerpsjablonen kunnen ook helpen bij het elimineren van dubbel werk dat meestal voorkomt bij toekomstige projecten. Deze aanpak bespaart honderden uren bij het ontwerpen en bouwen van machines. Een besparing van 20-40% op de investeringskosten kan worden gerealiseerd dankzij een snellere time-to-market, een hogere softwarekwaliteit en minder toekomstige uitvaltijd.
4. Hogere inbedrijfstellingssnelheid en prestatiezekerheid
60% van de inbedrijfstellingstijd wordt besteed aan het oplossen van problemen met besturingssoftware, protocollen en integratie. Veel van deze vertragingen kunnen echter worden vermeden door gebruik te maken van digitale modelleringstools. Ingenieurs hoeven niet langer te wachten tot de machine is gebouwd om inbedrijfstellingstaken uit te voeren. Tests kunnen digitaal worden uitgevoerd met alleen een PLC en het virtuele model. Virtueel testen van softwarebesturing, fabrieksacceptatietests (FAT) en inbedrijfstelling maken het eenvoudiger en goedkoper om systeemintegratie en evaluatie van softwarekwaliteit uit te voeren, aangezien deze niet langer in detail ter plaatse hoeven te worden uitgevoerd.
5. Soepeler machinegebruik
Digital twin-tools stellen OEM's ook in staat hun klanten post-installatiediensten aan te bieden die nieuwe inkomstenstromen kunnen genereren. Diensten zoals het trainen van operators, het testen van software-upgrades, het voorkomen van stilstand en het evalueren van de prestatie-efficiëntie helpen OEM's allemaal om een bredere relatie met hun klantenbestand op te bouwen. Diensten op afstand die mogelijk worden gemaakt door een digital twin, die ter plaatse op de productielocatie draait, parallel aan de echte machine, stellen OEM's, fabriekstechnici en operators in staat om precies aan te geven waar de efficiëntie kan worden verbeterd. Dit resulteert in minder ongeplande machinestilstand en een verbetering van de Overall Equipment Effectiveness (OEE) met 50%.
Gecombineerde efficiëntie zorgt voor snelheid van innovatie en ontwikkeling
Met EcoStruxure Machine Expert Twin digital twin-software kunnen ingenieurs de machines die ze ontwikkelen 20-50% sneller op de markt brengen. Ingenieurs kunnen het EcoStruxure Machine Expert Twin-platform gebruiken om verschillende combinaties van machinecomponenten uit te voeren en te zien hoe die verschillende opties het gedrag van de machine beïnvloeden. Dergelijke tools maken een gedurfdere en creatievere planning mogelijk, evenals een verbeterde uptime door superieur onderhoud van machines, een verbeterde winstgevendheid en een effectievere naleving van veranderende regelgeving.
Het EcoStruxure Machine Expert Twin-platform is gebaseerd op een open Microsoft.net framework dat eenvoudig kan worden aangepast aan de eisen van de eindgebruiker. Aangezien het platform gemakkelijk schaalbaar is, kunnen machinesimulaties worden uitgevoerd ongeacht de grootte, het type of de complexiteit van de machine. Om meer te weten te komen over hoe EcoStruxure Machine Expert Twin-software inspeelt op de hedendaagse vereisten voor machineontwerp, lees onze laatste whitepaper of bezoek onze website om een gratis proefversie te downloaden.
www.se.com
Nieuwe 3D digital twin-tools, zoals EcoStruxure Machine Expert Twin-platform van Schneider Electric, bieden waarde aan de interacties tussen OEM en eindklant in alle belangrijke fasen van de levenscyclus van machines:
1. Meer verkoop van machines
De 3D-animaties laten potentiële klanten in duidelijk detail zien hoe hun machines eruit zullen zien en hoe ze zullen werken voordat de machine is gebouwd. Dit krachtige hulpmiddel wekt de interesse van de klant en schept realistische gedeelde verwachtingen. Digitale "proof of concept"-activiteiten maken interactie met potentiële klanten en vroege validatie van machineontwerpconcepten mogelijk.
2. Betrouwbaarder machineontwerp
Het gebruik van kant-en-klare programmeerobjecten maakt het voor engineers eenvoudiger om een consistente machinekwaliteit te realiseren en biedt de flexibiliteit om ontwerpideeën eenvoudig te wijzigen en te valideren, zelfs voor zeer complexe automatiseringssystemen. Tijdens de O&O-ontwerp- en machineontwikkelingsfasen maakt virtual engineering gedifferentieerde, snelle machineontwerpen mogelijk met een verbetering van de ontwerpkwaliteit tot 30%.
3. Snellere machinebouw
De digital twin importeert eenvoudig data uit meerdere bronnen, zoals AutoCAD-systemen, Excel-spreadsheets, XML en vooraf gebouwde sjablonen uit eerdere projecten. Dankzij de multidimensionale database van de software is het niet meer nodig om honderden kopieën te maken binnen hetzelfde project. Het maakt grafische voorstellingen, statusconfiguraties, revisie datalagen en operationele parameters binnen hetzelfde projectbestand mogelijk. Referentieontwerpsjablonen kunnen ook helpen bij het elimineren van dubbel werk dat meestal voorkomt bij toekomstige projecten. Deze aanpak bespaart honderden uren bij het ontwerpen en bouwen van machines. Een besparing van 20-40% op de investeringskosten kan worden gerealiseerd dankzij een snellere time-to-market, een hogere softwarekwaliteit en minder toekomstige uitvaltijd.
4. Hogere inbedrijfstellingssnelheid en prestatiezekerheid
60% van de inbedrijfstellingstijd wordt besteed aan het oplossen van problemen met besturingssoftware, protocollen en integratie. Veel van deze vertragingen kunnen echter worden vermeden door gebruik te maken van digitale modelleringstools. Ingenieurs hoeven niet langer te wachten tot de machine is gebouwd om inbedrijfstellingstaken uit te voeren. Tests kunnen digitaal worden uitgevoerd met alleen een PLC en het virtuele model. Virtueel testen van softwarebesturing, fabrieksacceptatietests (FAT) en inbedrijfstelling maken het eenvoudiger en goedkoper om systeemintegratie en evaluatie van softwarekwaliteit uit te voeren, aangezien deze niet langer in detail ter plaatse hoeven te worden uitgevoerd.
5. Soepeler machinegebruik
Digital twin-tools stellen OEM's ook in staat hun klanten post-installatiediensten aan te bieden die nieuwe inkomstenstromen kunnen genereren. Diensten zoals het trainen van operators, het testen van software-upgrades, het voorkomen van stilstand en het evalueren van de prestatie-efficiëntie helpen OEM's allemaal om een bredere relatie met hun klantenbestand op te bouwen. Diensten op afstand die mogelijk worden gemaakt door een digital twin, die ter plaatse op de productielocatie draait, parallel aan de echte machine, stellen OEM's, fabriekstechnici en operators in staat om precies aan te geven waar de efficiëntie kan worden verbeterd. Dit resulteert in minder ongeplande machinestilstand en een verbetering van de Overall Equipment Effectiveness (OEE) met 50%.
Gecombineerde efficiëntie zorgt voor snelheid van innovatie en ontwikkeling
Met EcoStruxure Machine Expert Twin digital twin-software kunnen ingenieurs de machines die ze ontwikkelen 20-50% sneller op de markt brengen. Ingenieurs kunnen het EcoStruxure Machine Expert Twin-platform gebruiken om verschillende combinaties van machinecomponenten uit te voeren en te zien hoe die verschillende opties het gedrag van de machine beïnvloeden. Dergelijke tools maken een gedurfdere en creatievere planning mogelijk, evenals een verbeterde uptime door superieur onderhoud van machines, een verbeterde winstgevendheid en een effectievere naleving van veranderende regelgeving.
Het EcoStruxure Machine Expert Twin-platform is gebaseerd op een open Microsoft.net framework dat eenvoudig kan worden aangepast aan de eisen van de eindgebruiker. Aangezien het platform gemakkelijk schaalbaar is, kunnen machinesimulaties worden uitgevoerd ongeacht de grootte, het type of de complexiteit van de machine. Om meer te weten te komen over hoe EcoStruxure Machine Expert Twin-software inspeelt op de hedendaagse vereisten voor machineontwerp, lees onze laatste whitepaper of bezoek onze website om een gratis proefversie te downloaden.
www.se.com