www.technologieenindustrie.com
31
'22
Written on Modified on
Met oog voor detail naar de grootste verbetering van het jaar
Als wereldleider in oogzorg is voor Alcon alleen het beste goed genoeg. Zo ook als het gaat om het sealen van de plastic pouches, met daarin de toebehoren voor de oogchirurg. Dat sealen verliep goed, maar toch, wellicht kon het nóg efficiënter, zo vermoedden ze op de site in het Vlaamse Puurs. Dus werd contact gezocht met Panasonic Industry. En kwam het tot een visionoplossing die de locatie in Puurs het grootste besparingsproject in 2020 opleverde.
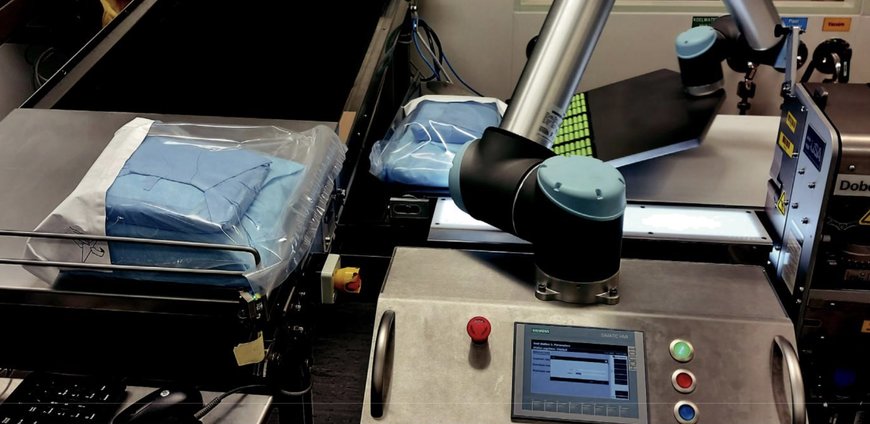
Met een nieuwe koers ontstaan andere mogelijkheden, ook voor een wereldleider als Alcon. Het van oorsprong Amerikaanse bedrijf is specialist in oogzorg, heeft productielocaties wereldwijd en splitste zich in 2019 af van farmaceut Novartis. Juist dat laatste zorgde voor een herijking, voor een frisse blik op de strategie. En dat is merk-baar, in elk geval op de productielocatie in Puurs, nabij Antwerpen. “Ons hoofdkantoor heeft uiteraard strikte doelen, maar het is heel nadrukkelijk aan onszelf om die hier binnen de mate van het mo-gelijke te verwezenlijken”, vertelt proces- en projectengineer Kevin Braeckmans. “Vergelijk ons met een jonge kmo, die z’n pad nog wat aan bepalen is. Dus moet je een plantrekker zijn, wil je binnen de overhead hier op de site goed kunnen functioneren.”
Aan ontwikkelingen geen gebrek, daar in Puurs. Alcon levert er binnenkort een nieuw gebouw op. En heeft bovendien nieuwe grond gekocht, vlakbij de huidige site. Mocht uitbreiding nodig zijn, dan is de ruimte er alvast. Want wie weet wat het productieportfolio nog gaat brengen, zegt Kristof Winkler, automation engineer voor de locatie in Puurs. “Neem alleen al onze producten voor vision care. Onze laboratoria werken daar voortdurend aan, onder andere voor de nieuwste lensdesigns.”
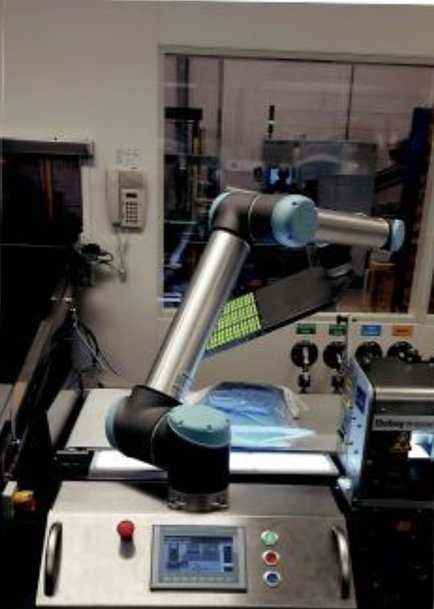
Steriel moet het zijn
Toch zal in Puurs de nadruk blijven liggen op medical devices, waar-onder Alcon Custom Paks. Het bedrijfsonderdeel levert kits voor oogchirurgen, die in de pouches de specifiek door hen gevraagde toebehoren vinden, zoals schorten, naaldjes en gaasjes. Maatwerk dus, wat vraagt om telkens weer de juiste samenstelling aan compo-nenten. En dat niet alleen: het pakket moet zo steriel mogelijk zijn, elke vervuiling is er één te veel.
Vandaar dus, dat Alcon zoveel waarde hecht aan een optimale sluiting van de pouches. Het bedrijf zette er tot voor kort twee medewerkers per lijn voor in: terwijl de ene medewerker het pakket sealde, con-troleerde de andere de sluiting tot in detail. Dat werkte in principe goed, stelt Kevin, niet voor niets wordt in Puurs volgens hem ge-streefd naar ‘de Rolls Royce van de chirurgische kits’. “En toch, zo dachten we: wat als we die controle konden automatiseren, daardoor medewerkers vrijmaken voor een andere rol in het proces en zo een besparing konden realiseren? Daarnaast speelde mee dat we het risi-co op verkeerd beoordeelde sealings nóg kleiner wilden maken. Onze medewerkers werken uiterst zorgvuldig. Maar toch, een fout maken is menselijk.”
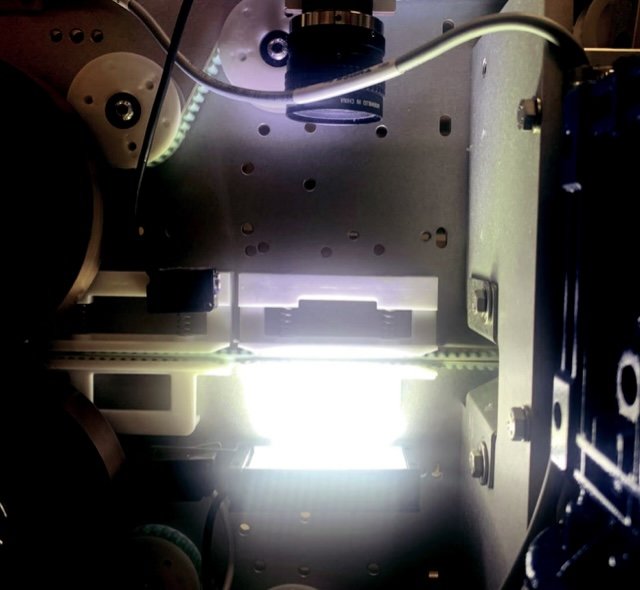
Alcon ging in eerste instantie een samenwerking aan met de Uni-versiteit Antwerpen, waar doctoraalstudenten een studie verrichtten naar de mogelijkheden om fouten in sealnaden te detecteren via visueel licht. En terwijl zij daarmee bezig waren, benaderde Alcon ook Panasonic Industry, dat voor de site al eens een visiontoepassing had geleverd. Een eerste gesprek in Puurs, met Panasonics key ac-countmanager Luc Aalders, zorgde voor voldoende aanknopingspunt-en. Waarna Kevin en Bart Peeters, plantmanager voor Alcon Custom Paks, eind 2019 langsgingen bij Panasonic in Best.
“Vanaf toen ging het snel”, blikt Kevin terug. “Panasonic heeft ons die dag in Best laten zien wat kan en ons daarmee overtuigd van het rendement van een visionoplossing. We kregen de bevestiging van wat ook de studenten van de universiteit ons inmiddels hadden laten weten: fullproofdetectie via een camerasysteem zou ons vrijwel zeker de juiste oplossing bieden.”
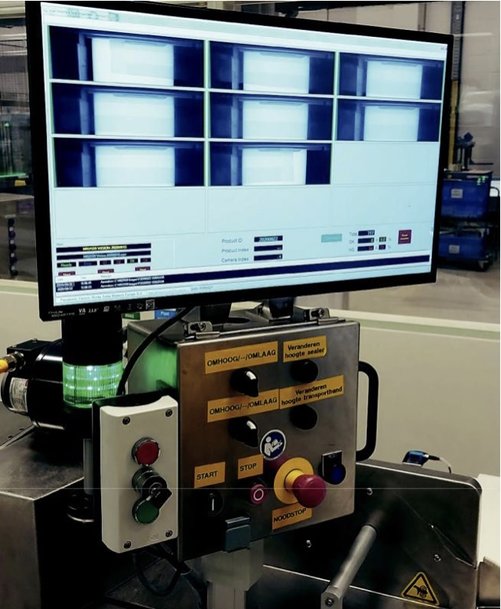
Testen in de praktijk
Namens Panasonic ging application engineer Roy Claessen begin 2020 langs in Puurs, om daar een camera op meerdere posities te plaatsen en zo te achterhalen welke plek voor optimaal stabiel beeld zorgt. Een positie net buiten de verpakkingsmachine bleek geen optie, daarvoor bewoog het product te veel. Dus stelde Roy voor de camera ín de machine te plaatsen, wat zorgde voor het gewenste resultaat.
Zie daar dan ook het nut van een test in de praktijk, vertelt Roy. “Testen in een laboratoriumopstelling biedt veel informatie, maar op basis daarvan een opstelling verkopen? Dat niet. Juist in de praktijk komen er andere aspecten bij kijken, volgen nog extra vragen en kom je zo samen tot de beste oplossing.” Bovendien, geen visionproject is hetzelfde, benadrukt Luc. “We weten inmiddels wel welke kant een project opgaat, maar hebben telkens te maken met nieuwe uitdagin-gen, wat ‘m vooral zit in het het materiaal van de klant. Zo ook bij Alcon: de pakketten zijn van plastic. Hoe reflecteert dat, hoe pakt de camera de beelden op? We willen ervan overtuigd zijn dat iets werkt.”
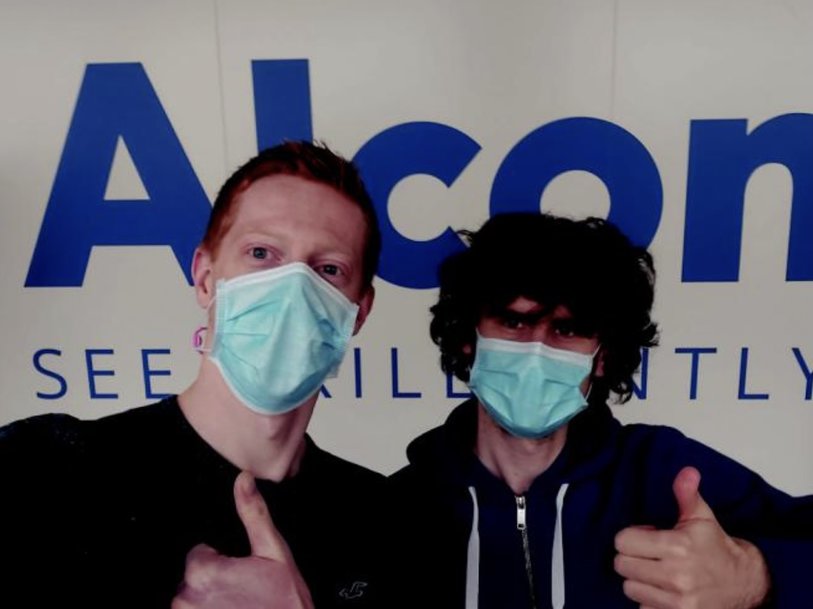
From left to right: Kevin Braeckmans Process & Equipment Improvement Engineer Kristof Winkler Process Engineer
En toen kwam corona
De test op locatie overtuigde Alcon zodanig, dat niet één, maar direct vier visionsystemen werden besteld. Niets stond een soepel verloop in de weg – en toen kwam corona. Waardoor werkzaamheden op locatie niet mogelijk waren, en een groot deel van het project op afstand en online moest gebeuren. Kristof: “Panasonic heeft ons alle hardware opgestuurd en online begeleid bij de installatie. Dat was voor niemand ideaal, maar het is wél gelukt. Dat maakt dit project extra bijzonder. De detectie verloopt zoals die moet doen, bovendien is Panasonic er ook nu voor ons. Ik heb na de installatie meerdere keren overlegd met Roy, leer het visionsysteem steeds beter kennen. Voor mij is dat erg waardevol.” Met de inzet van de vier systemen re-aliseert Alcon een fikse besparing, vertelt Kevin. “Sterker, dit project was voor ons de grootste besparing in 2020. De vier systemen ver-vangen samen 8 productiemedewerkers, het rendement is evident.”
Ook bij Panasonic wordt tevreden teruggekeken op het project. “Het was fijn dat we de machines net voor de pandemie nog hebben kun-nen zien”, vindt Roy. “Daardoor hadden we een volledig beeld, wisten we waar welk kabeltje liep en konden we op zoek naar de beste op-stelling. Zo ook voor de besturingskasten, die hun plek ónder in plaats van naast de sealmachines hebben.”
Naast corona was ook de tijdspanne een uitdaging, stelt Luc. “De bestelling kwam vlak voor de vakantie, dat vroeg om snel schakelen. Zo ook voor Evink Engineering, onze partner voor mechanica, dat de online begeleiding mee heeft verzorgd. Terwijl de mannen in Puurs met de camera in hun productieomgeving stonden, werd de mecha-nische opmeting door Evink via TeamViewer doorgegeven. Heel apart, ook voor ons. Of dit nou de optimale condities waren? Dat valt te betwisten. Maar we weten nu ook: het kán, dat hebben we bewezen. Alle betrokkenen waren flexibel genoeg om dit project, onder deze omstandigheden, tot een goed einde te brengen. Waarmee we hebben laten zien dat voor het beoogde resultaat het niet zozeer draait om werken voor de klant, maar vooral samen mét de klant.”
www.panasonic.com