www.technologieenindustrie.com
28
'19
Written on Modified on
Veiligheid eerst
Om ervoor te zorgen dat mensen en robots in gemeenschappelijke bewerkingszones zonder scheidingsbarrière harmonieus kunnen werken, moeten strenge veiligheidseisen in acht worden genomen.
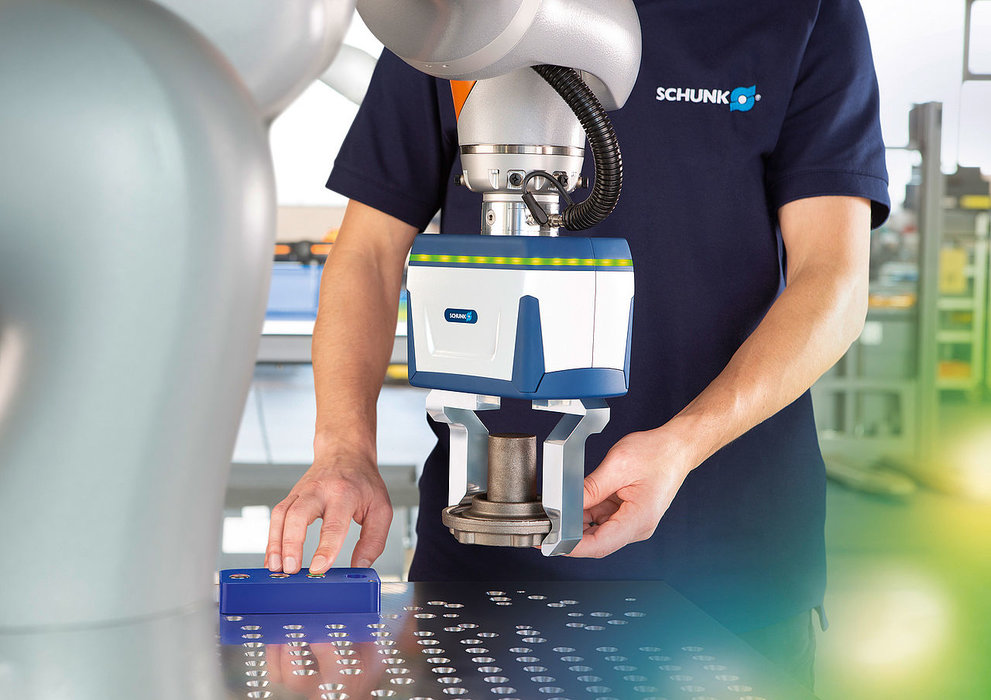
"HRC-toepassingen valideren is een bijzondere uitdaging", stelt prof. dr. Markus Glück, algemeen directeur Onderzoek & Ontwikkeling bij SCHUNK. Aan de gebruikerszijde bestaat er grote onzekerheid over hoe de gezondheids- en veiligheidsvereisten op de werkplek daadwerkelijk in richtsnoeren en normen moeten worden omgezet. "Voor een veilige samenwerking tussen mens en robot is niet alleen uitgebreide kennis van robottoepassingen vereist, maar ook expertise omtrent de risicobeoordeling", aldus Glück. Geen enkele HRC-toepassing is dezelfde, waardoor er telkens een individuele risicobeoordeling is vereist.
"Kracht, snelheid, bewegingstrajecten van de robot en in het bijzonder van het werkstuk, alsook de werkstukdrager, kunnen een gevaar vormen voor de operator." Deze gevaren moeten ofwel worden beperkt door inherente beschermingsmaatregelen te implementeren of, indien nodig, door aanvullende maatregelen om te beschermen tegen de risico's, benadrukt Prof. Dr. Glück. "Ons doel is om robotfabrikanten, integratoren en systeembouwers te voorzien van gedegen, onafhankelijk geteste componenten die ze kunnen gebruiken om samenwerkingsscenario's relatief snel te realiseren en te certificeren.
Gecertificeerde Co-Act-serie
De Co-act EGP-C-serie is gecertificeerd voor collaboratieve toepassingen en toont hoe dit eigenlijk in zjn werk gaat. Het grijperassortiment bestaat uit vier maten, is ontworpen voor eenvoudige handlingtaken en kan intuïtief worden geïnstalleerd op vrijwel alle gangbare lichtgewicht robots als Plug & Work-oplossing. "De meer dan 400 productinstallaties die momenteel bij klanten en partners staan, zijn een indrukwekkend bewijs van de maturiteit van de Co-act EGP-C," meldt Markus Glück.
De grijpkracht op de vinger, met een intrinsiek veilig ontwerp, is uit veiligheidsoverwegingen beperkt tot een maximum van 140 N. Krachtige programmeermodules en plug-ins zorgen voor een eenvoudige installatie. Gestandaardiseerde bevestigingsvingers met verwisselbare inzetstukken voor universeel gebruik maken het voor nieuwkomers gemakkelijker om hun eerste stappen te zetten in de wereld van de collaboratieve robotica. "Indien mensen en robots gemeenschappelijke bewerkingszones hebben, moeten de randen in deze zones worden afgerond, zodat mensen zich niet verwonden als de grijper erlangs schraapt of actief tegen de persoon drukt", benadrukt Glück. "Er moet ook worden vermeden dat de vingers en huid bekneld raken." Een duidelijke visualisering van de huidige bedrijfssituatie aan de hand van gekleurde leds schept vertrouwen.
Raadpleging tijdens de productontwikkeling
Met de co-act EGL-C gaat SCHUNK nog een stap verder. Met deze krachtpatser is het voor het eerst mogelijk geweest om een grijper te produceren voor collaboratieve toepassingen waarbij de grijpkracht op de vinger de grens van 140 N - die als niet schadelijk voor de gezondheid wordt beschouwd - overschrijdt. Net als bij de collaboratieve grijper voor kleine onderdelen SCHUNK Co-act EGP-C, hechtte SCHUNK ook veel belang aan de Deutsche Gesetzliche Unfallversicherung (DGUV), die ondersteuning biedt aan het productcreatieproces voor de Co-act EGL-C.
Deze samenwerking zorgde ervoor dat er al in een vroeg stadium communicatie mogelijk was en dat een efficiënte controle en observatie van de normen werd uitgevoerd. Daarnaast konden we leren hoe een gebruiksvriendelijke veiligheidsbeoordeling en certificering kan worden ontworpen, zonder afbreuk te doen aan de kwaliteit op het gebied van veiligheid. "Deze grijper beschikt over een zeer geavanceerd veiligheidsconcept", legt Prof. Dr. Glück uit. "Door tijdig te overleggen tijdens de ontwikkeling van de grijper konden we ervoor zorgen dat er vanaf het begin bijzondere aandacht werd besteed aan de naleving van de normen en de relevante wettelijke voorschriften bij de veiligheidselektronica, de veilige besturingstechniek en het veiligheidsconcept als geheel", stelt hij.
Grijpen in drie fasen
Een door SCHUNK ontwikkeld veiligheidsinformatiesysteem, waarvoor een patent is aangevraagd, verdeelt het grijpproces in de co-act EGL-C in afzonderlijke fasen. Zolang het gevaar bestaat dat menselijke handen of vingers bekneld kunnen raken, beperkt het geïntegreerde slimme systeem de grijpkracht tot een onschadelijke 30 N. De grijpvingers sluiten alleen met een vrij instelbare grijpkracht van maximaal 450 N. vanaf een werkstuk met een afstand van meer dan 4 mm, indien er geen gevaar voor beknelling bestaat.
Als het systeem voelt dat het in deze sluitingsfase meegeeft, bijvoorbeeld omdat er een werkstuk wordt vastgeklemd dat te klein is, en de operator het werkstuk met de hand wil verwijderen, wordt ook deze beweging automatisch gestopt. Hetzelfde geldt als de verwachte werkstukafmetingen met 2 mm worden overschreden, als er bijvoorbeeld geen onderdeel beschikbaar is.
In de derde fase herkent de grijper of het werkstuk veilig wordt vastgegrepen en wordt de rem aangespannen. De SCHUNK EGL-C voldoet daarmee aan de eisen voor een veilige samenwerking tussen mens en robot en garandeert dat de gegrepen componenten, die bij vormsluitend grijpen tot 2,25 kg kunnen wegen, ook in noodsituaties, en de daarmee gepaard gaande volledige remming, niet gelost worden. Bij vormsluitend grijpen is zelfs tot 8 kg mogelijk.
Modulair veiligheidsconcept als doelstelling
Toch is er nog veel werk aan de winkel op het gebied van certificering: "Om de mogelijkheden van HRC ten volle te kunnen benutten, is een oplossing nodig die zowel integratoren als operatoren in staat stelt om collaboatieve processen op eigen kracht te verwezenlijken met een redelijke inspanning.
Met inbegrip van validatie van de veiligheid en gezondheid op de werkplek", benadrukt Glück. Modulaire veiligheidsconcepten zoals voorgesteld door SCHUNK en waarop het bedrijf zich met zijn assortiment gecertificeerde grijpers richt, kunnen gebruikers oriënteren en de validatie van de veiligheid en gezondheid op de werkplek in individuele gevallen enorm vereenvoudigen. "Mochten gebruikers bij het ontwerpen van een mens/robot-werkplek kunnen rekenen op gecertificeerde componenten, zou de introductie van mens/robot-samenwerking in de dagelijkse productie aanzienlijk sneller gaan", legt Glück uit.
Ook de HRC-normgeving ontwikkelt zich volgens hem gestaag. Zo moet ISO/TS 15066 bijvoorbeeld uiterlijk na vier jaar worden herzien als technische specificatie. "Daarom is het belangrijk dat robotfabrikanten, aanbieders van grijpgereedschappen en eindeffectoren en integratoren actief met controle-instanties, zoals de DGUV, samenwerken aan de verdere ontwikkeling van de normen", aldus Glück. "Veiligheidsaspecten moeten hier en zonder compromissen voorrang krijgen. Tegelijkertijd zullen ze breder aanvaard worden als de veiligheid en moeilijkheidsgraad tijdens de installatie en certificering geharmoniseerd zijn".
Normen en richtlijnen voor de samenwerking tussen mens en robot
De wettelijke eisen voor samenwerkingsscenario's worden in eerste instantie beschreven in de EG-machinerichtlijn 2006/42/EG, bijlage 1: De fabrikant van een machine of zijn gevolmachtigde moet ervoor zorgen dat een risicobeoordeling wordt uitgevoerd om de toepasselijke gezondheids- en veiligheidseisen voor de machine te bepalen. De onmiddellijke omgeving van de toepassingen moeten in de analyse worden opgenomen voor de risicobeoordeling. Er moeten doeltreffende veiligheidsmaatregelen worden genomen tegen alle mogelijke schadelijke botsingen, met inbegrip van beknelling van ledematen, werkhandschoenen of werknemers die struikelen.
Normatieve referenties voor de functionele veiligheid van HRC-toepassingen zijn op hun beurt algemene normen, zoals IEC 61508, IEC 62061 en ISO 13849-1 en 2. Naast deze ISO 10218-1 en -2 moet de veiligheid van industriële robots in acht worden genomen. In de technische specificatie ISO/TS 15066:2017-04 worden in het bijzonder de belangrijkste gebruiksvereisten voor robots in collaboratieve toepassingen en robotica-apparatuur bepaald.
Deze "HRC-norm" beschrijft de gebruiksaanwijzingen voor vier soorten samenwerking en geeft een gedetailleerd uitleg van de vereiste veiligheidsprincipes. De norm bevat ook gedetailleerde specificaties over de pijndrempels die in acht moeten worden genomen voor de relevante delen van het lichaam.
www.schunk.com