Rondsels in plaats van riemen
Grindfabriek bespaart kosten en vermindert onderhoudsuitgaven door gebruik te maken van motorreductoren.
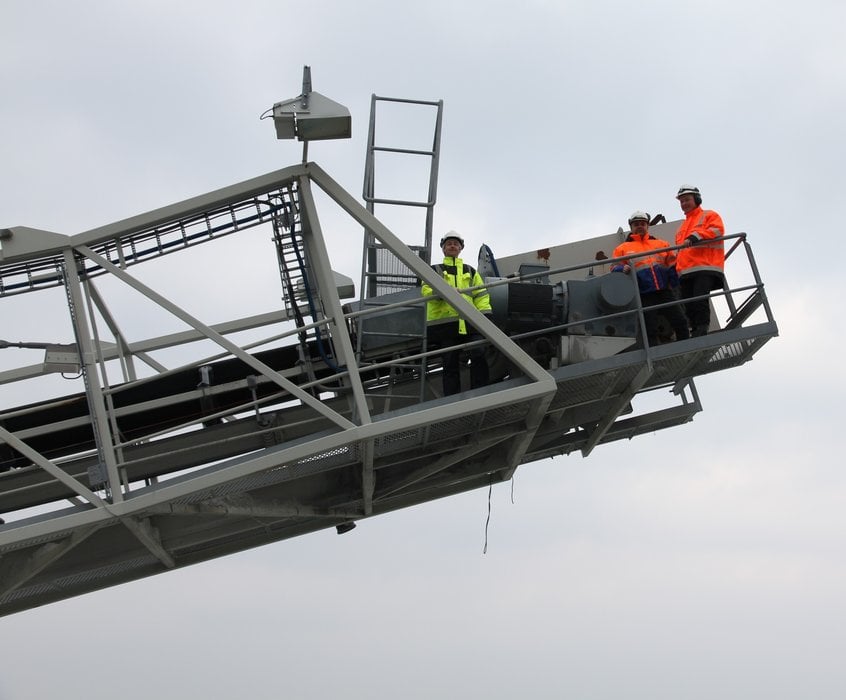
In veel grindgroeven, steenbreekinstallaties en soortgelijke installaties, wordt de drijfkracht voor transportbanden geleverd door riemaandrijvingen. Tot voor kort was dit ook het geval in de grindfabriek van NorStone AS in Tau, gelegen in het zuidwesten van Noorwegen. Onlangs besloot NorStone, een dochteronderneming van HeidelbergCement AG, over te gaan op robuuste motorreductoren. Deze optie beloofde lagere investeringskosten en een hogere operationele betrouwbaarheid, samen met een betere procesveiligheid. Ook werd gerekend op een gereduceerd energieverbruik dankzij een hogere efficiency.
NorStone is de grootste producent van grindproducten in Noorwegen. Het bedrijf levert toeslagmaterialen voor beton en asfalt, voor grindafdekking van pijpleidingen in kustgebieden en andere speciale producten. Elk jaar produceren de productiefaciliteiten van NorStone(tm) meer dan 6,6 miljoen ton grindproducten in diverse soorten en kwaliteitsklassen. De vraag is groot en zelfs met de huidige jaarlijkse productiecapaciteit van 2,3 miljoen ton van het materiaal kan de Tau plant nauwelijks voldoen aan de vraag. Dit maakt het vooral belangrijk om ervoor te zorgen dat de fabriek zoveel mogelijk operationeel is en ongeplande downtime te minimaliseren.
Duidelijke voordelen, plus een hogere betrouwbaarheid met directe aandrijvingen
Motorreductoren zijn in feite niet nieuw in grindgroeven. Directe aandrijvingen van dit type werden vaak gebruikt in de jaren tachtig maar in de daaropvolgende jaren stapten vele plants over op riemaandrijvingen omdat de reserveonderdelen voor deze aandrijvingen altijd snel beschikbaar waren terwijl producenten en leveranciers van motorreductoren niet in staat waren om op dezelfde snelle wijze reserveonderdelen te leveren.
"We hebben geconstateerd dat onderhouds- en reservedelen voor motorreductoren inmiddels zeer snel leverbaar zijn. We houden zelf een aantal onderdelen op voorraad en voor de rest hebben wij het volste vertrouwen in NORD Drivesystems als leverancier," geeft Ivar Ullestad, Maintenance Manager bij Tau als reden om terug te gaan naar de eerdere oplossing. "Hiermee kunnen we de bekende voordelen van aandrijfoplossingen met motorreductoren ten volle benutten. Met name de direkt aangebouwde aandrijving leidt tot een hogere betrouwbaarheid, hetgeen minder downtime en dus minder verloren productietijd betekent. Een ander belangrijk aspect is dat er minder onderhoud nodig is. Naast het verminderen van de onderhoudskosten, verhoogt dit de veiligheid in de fabriek," voegt Ullestad toe.
Aantoonbaar minder slijtage dan bij assen en riemen
Arbeidsomstandigheden zijn een belangrijke factor bij dergelijke overwegingen. "Je moet je realiseren dat we het hele jaar door buiten werken. Het merendeel van de locaties van de transportbandaandrijvingen zijn open en onbeschermd. Vanwege de barre weersomstandigheden in het westen van Noorwegen, met veel wind, regen en natte sneeuw, maar ook door de stoffige en nogal onplezierige omgeving ter plaatse, proberen we de reparatie- en onderhoudstijden voor onze onderhoudsdienst zo kort mogelijk te houden."
De Tau fabriek draait zeven dagen per week, 24 uur per dag in ploegendienst. De 168 productie-uren omvatten 16 uur aan gepland onderhoud. De fabriek is alleen tijdens de winterstop gesloten. Tijdens deze stop worden in twee tot drie weken de jaarlijkse onderhoudsinspectie en de revisietaken uitgevoerd. De direkt aangebouwde aandrijvingen hebben bijgedragen aan een duidelijke verbetering van de betrouwbaarheid, wat neerkomt op ongeveer 4,5 procent, gedurende de laatste drie jaar.
"We zijn erg tevreden met deze trend. Met de overstap van de as- en riemaandrijvingen op de direct drives met motorreductoren van NORD Drivesystems, elimineren we in de eerste plaats het aspect van riemslijtage, die aanzienlijk is. Voorts kan er geen water of stof in het aandrijfmechanisme terecht komen. Dit alles betekent dat de beslissing voor compacte, robuuste motorreductoren duidelijke voordelen oplevert, waarmee bewezen is dat het een juiste beslissing is geweest," vat Per Don, Productie Manager van de NorStone plant samen. De directe aandrijvingen hebben meer opgeleverd dan alleen maar hogere betrouwbaarheid en lagere (arbeid)kosten voor onderhoud. De relatieve investeringskosten voor de aanschaf van nieuwe reductoren bleken ook lager uit te vallen. Het vervangen van een compleet pakket, bestaande uit een met een as uitgevoerde unit inclusief riemschijven, riemen, een afdak, riemafdekking en motor, bleek duurder dan de aanschaf van een vergelijkbare motorreductor.
Aangezien een serie periodieke vervangingen van motorreductoren toch al gepland stond, was een uitgebreide overstap van as- en riemaandrijvingen naar direkt aangebouwde aandrijvingen voor Ullestad een logische keuze. Men werkt momenteel aan de standaardisatie van aandrijfcomponenten. "In het kader van de geplande bezuinigingen bij de aandrijfsystemen van de transportbanden, zijn we druk bezig met het standaardiseren van aspecten als motor- en asafmetingen en de trommeldiameter, teneinde de diversiteit te beperken en zo het onderhoud, het voorraadbeheer en de service te vereenvoudigen. We ontwikkelen ook back-up oplossingen, dat onder meer het zelf op voorraad houden van componenten betreft," aldus de maintenance manager.
NorStone AS
Het Noorse bedrijf NorStone AS (http://www.norstone.no/) is een volwaardige dochter van HeidelbergCement AG, een van 's werelds grootste producenten van bouwmaterialen als cement, zand en grind. De fabriek in Tau doseert, mixt, controleert en levert kwalitatief hoogwaardige toeslagmaterialen voor beton en asfalt, alsmede funderingsmaterialen met een constante kwaliteit in verschillende gradaties. De materialen worden gesplitst en gehakt in gekalibreerde maten, waarna ze worden vermengd tot maatverdelingen die voldoen aan de specifieke eisen van de klant. Tijdens dit proces wordt de naleving van EU-normen gecontroleerd door eigen laboratoria. NorStone levert onder andere funderingsmateriaal voor de spoorwegindustrie, wegenbouwmaterialen en bindlaagmateriaal voor kustgebieden. De Tau fabriek produceert 2,3 ton materiaal per jaar, waarvan ongeveer 75% wordt geëxporteerd.
Figuur 1: De NorStone plant.
Figuren 2 en 3: De NorStone plant gebruikte vroeger vele graaftransportbanden, zoals links op de foto, die verbonden waren met een as- en riemaandrijving en twee 55 kW motoren. De gerenoveerde transportbanden zijn daarentegen uitgerust met motorreductoren, zoals de combinatie van een SK 9086.1 motorreductor en de 90-kW motor rechts op de foto.
Figuur 4: De Tau plant is gelegen pal naast de oceaan en beschikt over een eigen aanlegsteiger, die elk jaar 700 tot 900 schepen kan ontvangen. De beladingsband is uitgerust met een 37 kW motor en een SK 9082.1-225S/4 motorreductor.
Figuur 5: Zware en vooral stoffige omstandigheden: een 15 kW aandrijving met een SK 9052.1-160L/4 motorreductor is gemonteerd onder de breekmachine op band 10.