www.technologieenindustrie.com
30
'09
Written on Modified on
Verbeterde kwaliteit bij lasreparatie van raildefecten door Tata Steel met lagere kosten
Tata Steel Rail heeft een nieuwe techniek ontwikkeld voor de kosteneffectieve reparatie van discrete defecten op railoppervlakken. De belangrijkste kracht van deze nieuwe techniek betreft de vervanging van die aspecten van het conventionele booglasproces (MMA) die vaak variaties veroorzaken in de kwaliteit van de reparatie, door automatische en meer gecontroleerde processen. Bij het ontwikkelde semi-automatische proces wordt openbooglassen met gevulde draad toegepast, waarbij wordt voorverwarmd bij een lage temperatuur teneinde pro-actief de metallurgische transformaties binnen de warmtebeïnvloede zone (WBZ) te kunnen controleren. Ervan uitgaande dat de gemiddelde kosten per reparatie of vervanging van een stuk rails kunnen oplopen tot meerdere duizenden euro’s en dat het ontstaan van wiel/rails oppervlaktedefecten waarschijnlijk zal toenemen met de verwachte groei van de verkeersintensiteit op de meeste spoorwegen, is het belang van het nieuwe proces makkelijk te begrijpen.
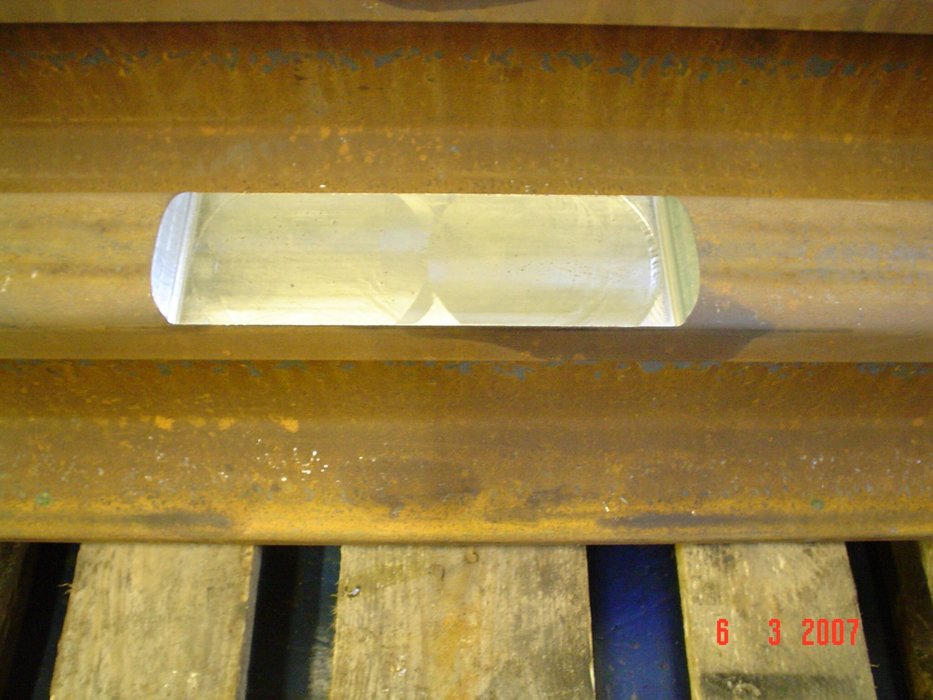
Het rollen van treinwielen over rails zorgt voor patronen van hoge en complexe spanningen op het rail/wiel contactvlak, die leiden tot degradatie van het oppervlak. Het brede scala aan baanontwerpen, wielprofielen en soorten verkeer kan resulteren in een veelheid aan oppervlaktefouten die de levensduur van de rails reduceren.
Gebreken zoals squats en wheelburns komen zelfs in de meest moderne en goed onderhouden spoorwegnetten voor en doorgaans krijgt elk netwerk eens per jaar om de twee kilometer met één van zulke gebreken te maken. De vervanging van zulke defecten door een kort stuk rails is duur en niet altijd wenselijk, omdat dit twee nieuwe discontinuïteiten in de rails introduceert in de vorm van twee aluminothermische lassen (exotherme reactie met behulp van aluminium als reduceermiddel) die de voordelen van lange warm opgerolde rails (tot 120 meter) teniet doen. De alternatieve conventionele techniek voor het repareren van dergelijke defecten is het booglasproces (MMA). Hoewel deze techniek wordt gebruikt in een groot aantal industrieën, is ze sterk afhankelijk van de competentie van de lasser, tijdrovend en gevoelig voor interne defecten, zoals poreusheid, die vervolgens vermoeiïng veroorzaken, en, indien niet gedetecteerd door ultrasone inspectie, resulteren in railbreuk.
De volgende factoren dragen bij aan de kosteneffectiviteit en het technische fundament van het nieuw ontwikkelde proces:
1. Het verlagen van de traditionele voorverwarmtemperatuur van 350°C naar slechts 80°C heeft als voordeel dat de reparatie sneller kan worden uitgevoerd, de diepte van de warmtebeïnvloede zone kleiner wordt, en een meer robuuste microstructuur wordt verkregen.
2. De toepassing van een gestandaardiseerde verwijdering van het aangetaste gebied door gecontroleerd slijpen heeft als voordeel dat het reproduceerbaar is en niet afhankelijk is van het subjectieve oordeel van de operator.
3. Toepassing van een geprogrammeerd halfautomatisch openbooglasproces met gevulde draad garandeert een gecontroleerde warmtetoevoer en voorspelbare lastijden.
De kwaliteit van het, met het nieuw ontwikkelde lasproces gerepareerde loopvlak wordt gegarandeerd doordat de reparatie zeer vermoeiïngsbestendig is en doordat het een vergelijkbare slijtvastheid heeft overeenkomstig de standaard Grade R260 rail, met een uniforme hardheid en een uniforme microstructuur in het door de las gerepareerde stuk rails.
De nieuwe gepatenteerde reparatietechniek van Tata Steel is opgebouwd uit vier stappen:
Het defect wordt eerst verwijderd met behulp van een draagbare drieassige freesmachine die om de zijkanten van de rails wordt geklemd. Hiermee wordt het geconstateerde defect uitgefreesd. Dit is op zich een aanzienlijke verbetering ten opzichte van het handmatige slijpen of snijbranden, die allebei een niet consistente holtevorm of oppervlakteafwerking geven om geprogrammeerd automatisch lassen mogelijk te maken.
Ten tweede worden de aangrenzende zone en de holte voorverwarmd met een conventionele brander. Voor Grade 260 rails ligt de voorgeschreven temperatuur tussen 60 en 80°C. De keuze voor deze temperatuur is gebaseerd op het kunnen beheersen van de microstructuur in de WBZ en het ingeprogrammeerde haakse depositiepatroon van de achtereenvolgende/aangrenzende lassen zorgt ervoor dat de microstructuur in de HAZ bestaat uit fijn perliet en vrij is van verbrossend martensiet. Deze temperatuur is geschikt voor de meeste railstaalsoorten met hoog koolstofgehalte die tegenwoordig worden toegepast, maar dient mogelijk te worden aangepast bij stalen met andere transformatie-eigenschappen, zoals laagkoolstof carbidevrije bainitische staalsoorten.
In de derde fase wordt gebruik gemaakt van een halfautomatische lasreparatiemachine met een openbooglasproces, Network Rail (UK) goedgekeurd TN3-0 lasmateriaal en voorgeschreven lasparameters. De positionering van de bovenste laag is cruciaal om het ontstaan een nieuwe warmtebeïnvloede zone te voorkomen. De grootste deel van de bovenste laslaag wordt gedeeltelijk verwijderd door profielslijpen.
De vierde en laatste stap bestaat uit het herstellen en het in elkaar laten overlopen van het dwars- en lengteprofiel van de rail door te slijpen met behulp van conventionele spoorslijpmachines.
Een vergelijkende evaluatie van de bestaande MMA techniek en het nieuwe proces werd gedaan door de thermische geschiedenis van beide processen vast te leggen met behulp van ingebedde thermokoppels. Verschillende belangrijke conclusies staven de metaalkundige robuustheid van het proces:
- Ondanks dat er maar tot 80°C wordt voorverwarmd, blijft de temperatuur in de WBZ na elke lasgang boven de 200°C waardoor transformatie in de martensitische microstructuur wordt voorkomen (aangezien de overgangstemperatuur van martensiet 160°C is voor Grade 260 rails).
- De afkoelsnelheden in het ontwikkelde proces zijn ongeveer gelijk aan die in het conventionele MMA proces voor alle laslagen behalve de eerste. De hogere snelheid van 5.2°C/s na de eerst aangebrachte las is eveneens de helft van de kritische snelheid voor de transformatie in martensiet.
- Een scheurvrij laslaagoppervlak wordt gerealiseerd, met een volledig perlitische microstructuur, vrij van martensiet en bainiet.
- Uit het hardheidsprofiel blijkt dat de slijtvastheid van de bainitische laslaag vergelijkbaar is met die van Grade R260 rails en zal zorgen voor een goed lengteprofiel.
- De laslaag werd onderworpen aan een buig-/vermoeiïngstest met een toegepaste spanningsrange van drie keer de verwachte spanning in bedrijf. Vijf miljoen cycli werden met succes voltooid, zonder breuk. Dezelfde laag doorstond nog eens met succes 4,3 miljoen cycli bij een toegepaste spanning van acht maal de verwachte spanning.