www.technologieenindustrie.com
21
'20
Written on Modified on
Duurzaam produceren
Bedrijven plakken tegenwoordig het label “duurzaam” op allerlei producten en activiteiten, van vis en meubels tot energieverbruik en architectuur. Daarbij gaat het hen, zoals ze zelf aangeven, om milieubescherming en het behoud van natuurlijke hulpbronnen. Ook bij het bewerken van materialen als onderdeel van de productie is altijd al gestreefd naar duurzaamheid, maar dan in een meer specifieke zin. Wanneer een fabrikant erin slaagt materiaal te bewerken tot scherp geprijsde, hoogwaardige producten, dan kan hij winst maken en zo zijn bedrijf in stand houden.
Sinds jaar en dag proberen fabrikanten manieren te vinden om hun bewerkingsprocessen efficiënter en rendabeler te maken, zoals het constant ontwikkelen van geavanceerde en nauwkeurige productiemachines, het verbeteren van snijgereedschappen en het optimaliseren van snijsystemen in het algemeen. Voorbeelden van specifieke strategieën op dit gebied zijn hogesnelheidsverspanen, hoge-voeding-verspanen, verspanen met hoge prestaties en het toepassen van digitalisering.
Het nieuwe initiatief dat bekend staat als duurzame materiaalbewerking heeft als doel het verbruik van grondstoffen en energie, en het genereren van afval gedurende de hele levenscyclus van het product te beperken tot een niveau dat op zijn minst in balans is met de draagkracht van onze planeet. Algemene discussies over duurzaamheid concentreren zich vaak op grote wereldwijde milieuvraagstukken, waarbij echter basale zaken op het gebied van prijs, kosten, klanttevredenheid, proceskennis en betrouwbaarheid over het hoofd worden gezien. Als het gaat om duurzaamheid bij het bewerken van materialen, begint werkelijk succes met eenvoudige, ongecompliceerde analyses en acties.
Duurzaamheid bij het bepalen van prijzen
Ieder bedrijf krijgt te maken met de uitdaging om voor zijn goederen of diensten prijzen te bepalen die ook op de langere duur aanvaardbaar zijn. De prijs moet hoog genoeg zijn om de kosten te dekken en winst op te leveren, maar laag genoeg om te voorkomen dat de klanten naar de concurrentie stappen. Als de klant vindt dat het product voldoende waar voor zijn geld biedt, kan de prijs die door de fabrikant gevraagd wordt ook hoger uitvallen.
Aan de andere kant, als onder druk van klanten en concurrentie een te lage prijs wordt gevraagd, gaat dat ten koste van de winstmarge. Is de prijs lager dan de productiekosten van het product, dan levert dat verlies op. Als onder druk van de concurrentie de prijs te laag uitvalt, moeten degenen die het product ontwerpen en bewerken manieren vinden om het goedkoper, sneller en beter te vervaardigen om de productiekosten te verlagen en tot een winstmarge te komen die ook op de langere duur aanvaardbaar is.
Onzichtbare kosten
In veel bedrijven is echter niet duidelijk waar de kosten stoppen en de winst begint. Dat komt doordat de werkelijke kosten zelf ook onduidelijk zijn. Verborgen, genegeerde of onbekende factoren worden in de kostenberekening niet meegenomen. Typische onzichtbare kosten zijn ongeplande downtime, afgekeurde werkstukken en defecte gereedschappen. Deze kosten worden niet als representatief of "reëel" gezien. Deze manier van denken leidt ertoe dat bepaalde kostenfactoren onzichtbaar worden, en is niet beperkt tot het productiepersoneel; hij kan door het hele bedrijf heen voorkomen.
Om tot een duurzame kostenstructuur te komen, moet het onzichtbare zichtbaar worden gemaakt. Het productiepersoneel moet het bewerkingsproces en tevens de structuur en de stroom van de organisatie-activiteiten in het algemeen onderzoeken en evalueren om verborgen kosten te ontdekken.
Klanttevredenheid
Klanttevredenheid is een wezenlijk element van economische duurzaamheid. De klant wil weten wanneer zijn of haar bestelling aankomt. In het hoofd van de klant begint de levertijd op het moment dat hij een bestelling plaatst. En levertijd is meer dan alleen maar de productietijd. Als het bewerken van een onderdeel drie weken in beslag neemt, maar het administratieproces kost nog twee weken extra, dan moet de fabriek zo eerlijk zijn - zowel tegenover zichzelf als tegenover zijn klanten - om een levertijd van vijf weken op te geven. Leveranciers van metaalbewerkingsgereedschappen zoals Seco Tools bieden systemen aan voor gereedschapsvoorraadbeheer, gereedschapsidentificatie en het monitoren van machines, waarmee het werkplaatspersoneel de voortgang van het werk dat voor een bepaalde klant wordt verricht kan bewaken en die producenten in staat stellen hun gewenste doorlooptijd aan te houden en hun klanttevredenheid te maximaliseren. (Zie kolom zijkant)
Afval en het belang van meten
Bij efficiënt produceren worden er zo weinig mogelijk tijd, energie en grondstoffen verspild. De afvalproducten van materiaalbewerking, zoals spanen, snij-oliën en koelvloeistof, zijn een complex vraagstuk. Van oudsher beschouwen fabrikanten afvalproducten als iets wat het proces onvermijdelijk met zich meebrengt en geloven ze dat het moeilijk is daarin verandering aan te brengen en dat het daarom altijd min of meer zo gebleven is. In de materiaalbewerking wordt veelal gedacht: “Niets aan te doen, op een andere manier het gaat het nu eenmaal niet."
Voor het effectief minimaliseren van afval en het behouden van hulpbronnen is een grondig inzicht in bewerkingsprocessen en in de kenmerken van werkstukmaterialen nodig. Voor het verkrijgen van dat inzicht moeten de procesfactoren nauwkeurig worden gemeten om precies te bepalen wat er wordt gedaan en welke resultaten dat daadwerkelijk oplevert. Bij echte nauwkeurigheid horen geen ronde getallen; ronde getallen wijzen meestal op een gebrek aan kennis van het betreffende proces en belemmeren een valide bepaling van de resultaten van veranderingen. Als een fabriek beweert dat de productie-efficiëntie "hoger is dan 60 procent", is dat dan 61 procent of 95 procent? Beide zijn nu eenmaal hoger dan 60 procent. En een snijsnelheid van "ongeveer 200 m/min" is geen betrouwbare opgave. De snelheid zal eerder 195 m/min of 206 m/min bedragen dan een of ander geschat rond getal.
In één geval was een fabrikant ervan overtuigd dat zijn bedrijf 70 procent (een rond getal) van de beschikbare tijd gebruikte voor materiaalbewerking. Uit een zorgvuldige meting bleek dat dit in werkelijkheid slechts 34 procent was. Simpel gezegd: van elke drie machines in die fabriek was er een in bedrijf en stonden er twee stil. De onzorgvuldige meting (gissing) van de fabrikant bleek dus eigenlijk waardeloos.
Duurzaamheid en salarissen
Bij het analyseren van duurzaamheid in relatie tot arbeidskosten wereldwijd moeten bij het beoordelen van de arbeidsproductiviteit salariskosten buiten beschouwing worden gelaten. De arbeidsproductiviteit is gelijk aan de hoeveelheid productie minus de kosten van ingekochte goederen en diensten, gedeeld door het aantal werknemers, gedeeld door een tijdseenheid.

Figure 1:
HQ_ILL_Labor Productivity.jpg
Deze formule meet de arbeidsproductiviteit zonder invloed van de personeelskosten en maakt het mogelijk op een geldige manier de arbeidsproductiviteit in landen of bedrijven met verschillende salarisschalen te vergelijken. Het salaris van een geschoolde machine-operator in een westers land, bijvoorbeeld, is misschien tien keer zo hoog als dat van een operator in een lage-lonen-land, maar dat verschil zegt niets over hun werkelijke productiviteit. Het is best mogelijk dat de 10 operators in het lage-lonen-land minder onderdelen produceren, met een lagere kwaliteit, dan die ene operator in het westen.
Als echter de daadwerkelijke arbeidsproductiviteit (zoals hierboven gemeten) in het lage-lonen-land op het hetzelfde niveau ligt als in het westerse land, dan is het om te komen tot economisch duurzame productiviteit in het westen nodig om te investeren in innovatieve technologie en productiemethodes, en in de permanente scholing van het productiepersoneel.
Een hoge arbeidsproductiviteit wijst erop dat het productiepersoneel een grondig inzicht heeft in de eigen werkzaamheden en over uitgebreide kennis en vaardigheden beschikt. Hierdoor kunnen ze sneller werken, hun volledige competentie benutten en zijn ze tevredener met hun baan. Voor een vakbekwame operator is het bij het bewerken van materiaal frustrerend om met onverwachte zaken geconfronteerd te worden. Dit komt vaak voor bij de huidige High Mix Low Volume-productie, aangezien de producten en het volume van de kleine partijen die worden geproduceerd zeer snel veranderen. Vakbekwame, multidisciplinaire operators zijn echter in staat snel hun manier van werken aan te passen om knelpunten en andere storende gebeurtenissen te overwinnen.
Betrouwbare processen
Een duurzaam bewerkingsproces is betrouwbaar en voorspelbaar, en minimaliseert energieverspilling. Een onbetrouwbaar proces leidt er toe dat bewerkingen moeten worden overgedaan, dat werkstukken worden afgekeurd en zorgt voor verspilling van de grondstoffen, energie en arbeid die nodig waren voor de afgekeurde producten.

Figure 2:
HQ_ILL_Next Step Streams In And Around A Machining Process.jpg
Op dezelfde manier is Work in Process (WIP) - onderhanden werkstukken - vanuit het oogpunt van duurzaamheid eigenlijk verspilling. Vanuit economisch oogpunt betekenen onderhanden werkstukken verloren geld, verloren tijd en verspilde vloerruimte. Bovendien is er altijd de mogelijkheid dat een opgeslagen halffabricaat beschadigd raakt terwijl het door het logistieke systeem gaat. Daarom moet een fabriek zo weinig mogelijk WIP hebben.
Minder energieverbruik
In de loop van de geschiedenis zijn er diverse manieren gevonden om bij het produceren betere resultaten te bereiken met minder energie. Aan het begin van de jaren tachtig stonden er in veel werkplaatsen bijvoorbeeld machines met een vermogen van 70 kilowatt of meer. Tegenwoordig is het mogelijk om met freesmachines met een vermogen van 7 kilowatt een hogere productiviteit te behalen dan met de oude, tien keer zo krachtige machines. Een duurzaam verspaningsproces minimaliseert het energieverbruik per kubieke mm of kubieke inch verwijderd materiaal. Het minimaliseren van het energieverbruik leidt automatisch tot minder energieverspilling, waardoor het bewerken van materiaal milieuvriendelijker wordt.
Maximale efficiëntie
Afbeelding 3 toont het stroomverbruik voor één werkdag van een 5-assig bewerkingscentrum. (Deze gegevens zijn afkomstig van slechts één machine en worden gebruikt als algemene referentie.) Verrassend genoeg gaat het grootste deel van de energie die de machine verbruikt niet naar de hoofdspindel. De aandrijfmotoren van de hoofdspindel en de as verbruiken normaal slechts 30 procent van de energie, terwijl verschillende koelsystemen 44 procent gebruiken en pompen, transformatoren, de machinebesturing en andere systemen de rest verbruiken. Als de machine niet aan het snijden is, blijven de meeste andere systemen dus energie verbruiken.
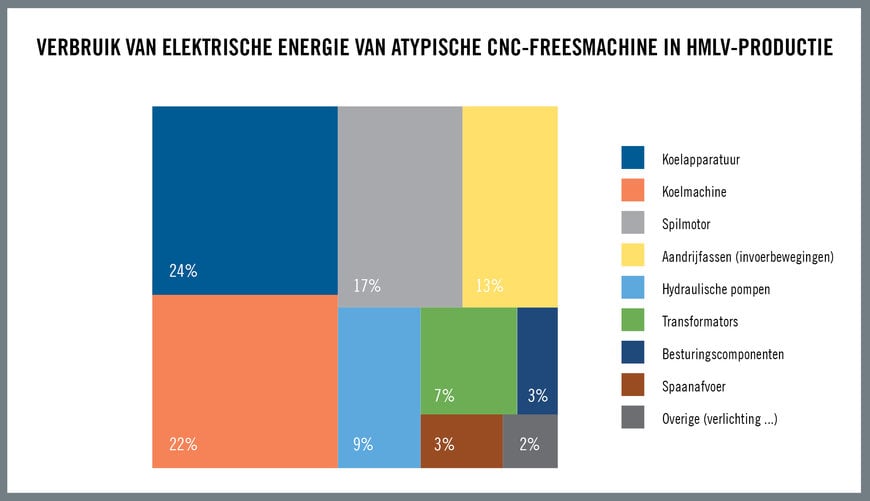
Figure 3:
HQ_ILL_Consumption Of Electrical Energy Of Atypical CNC Milling Machine In HMLV Production.jpg
Efficiënt energiegebruik kan de output van producten aanzienlijk verhogen met een minimale toename van het totale energieverbruik. In één scenario duurt het daadwerkelijk bewerken van een onderdeel één uur. Als het programmeren, instellen en de wachttijd zes uur in beslag nemen, produceert de machine twee onderdelen in een dag van acht uur. Wanneer de machine aan het snijden is, kan het energieverbruik worden beschouwd als 100 procent of nominaal één eenheid. Voor het snijden wordt 20 procent van de energie verbruikt, dus wanneer de machine niet aan het snijden is, verbruikt hij 80 procent van een energie-eenheid. Dus bedraagt het totale energieverbruik gedurende de dag 6,8 eenheden terwijl de machine twee onderdelen produceert.
In een tweede scenario wordt het proces geanalyseerd met speciale aandacht voor het elimineren van tijdverspilling. De analyse maakt het mogelijk om de inactieve tijd terug te brengen tot 5 uur, een vermindering van 16,5 procent. Er is nu drie uur snijtijd beschikbaar gekomen, waardoor er drie onderdelen geproduceerd kunnen worden. Het totale energieverbruik per dag is 7 eenheden, oftewel 3 procent meer dan in scenario één.
Het produceren van één werkstuk in scenario één vereist 3,4 energie-eenheden, terwijl in scenario twee de productie van elk werkstuk 2,2 eenheden energie vereist. Het energieverbruik per werkstuk in scenario twee neemt met 36 procent af bij een toename van het dagelijkse energieverbruik van slechts 3 procent. Voor het produceren van drie werkstukken in scenario één zou de machine langer moeten draaien en meer energie moeten verbruiken. Duurzame materiaalbewerking houdt niet zo zeer in dat er minder energie verbruikt wordt, maar betekent dat er met de verbruikte energie meer gedaan wordt.
Conclusie
Fabrikanten hebben lange tijd gestreefd naar economische duurzaamheid door materiaal te bewerken tot scherp geprijsde, hoogwaardige producten die hen in staat stellen hun bedrijf te onderhouden en het bestaan ervan te verzekeren. Economische duurzaamheid bestaat uit vele componenten, maar over het algemeen zijn deze eenvoudig en ongecompliceerd. Ze draaien vooral om realistisch, eerlijk en nauwkeurig evalueren en om het elimineren van verspilling in alle aspecten van het productieproces.
Fabrikanten die economische duurzaamheid tot stand brengen, slagen er ook in de impact van hun activiteiten op het milieu aan te pakken en te verminderen en zo duurzaamheid te bereiken in planetaire zin.
(Kolom zijkant)
Meten en duurzaamheid
Het organiseren en meten van procesfactoren en apparatuur vormt een belangrijke stap in het elimineren van verspilling en het tot stand brengen van duurzame materiaalbewerkingsprocessen. Om precies te weten waar er sprake is van tijd- en energieverspilling moet het productiepersoneel werken met exacte getallen en feiten, in plaats van speculaties en ronde schattingen.
Op het meest elementaire niveau moet het productiepersoneel weten welke gereedschappen beschikbaar zijn en waar de gereedschappen zich in de fabriek bevinden. Als die informatie niet beschikbaar is, gaan medewerkers gissen, veronderstellingen doen en gaan ze op zoek naar de gereedschappen. Dit is de zogenaamde werkplaats-safari. Het personeel weet dat de gereedschappen ergens in de werkplaats zijn, maar niet precies waar.
Seco Tools biedt gereedschapsidentificatie- en managementsystemen aan die zijn bedoeld om een einde te maken aan de werkplaats-safari. Het Seco Inventory Management System, bijvoorbeeld, is een veelzijdig, industrieel distributiesysteem dat volledig in de productiestroom van een fabriek kan worden opgenomen. Nadat Inventory Management is geconfigureerd met de specifieke gereedschapsbehoeften van de fabriek, levert het automatisch uitgebreide rapportages om het gebruik van de gereedschappen te volgen en onregelmatigheden op te sporen die op problemen kunnen wijzen.
Het is ook van essentieel belang dat gereedschappen correct worden geïdentificeerd terwijl ze door het productieproces gaan. Identificatie op zicht en op gevoel is niet altijd genoeg wanneer er sprake is van een groot aantal min of meer gelijk-uitziende gereedschappen. Seco Tools werkt samen met IDEM bij het aanbieden van een digitaal gereedschapidentificatiesysteem dat gebruik maakt van RFID-tags (Radio Frequency Identification) en een Bluetooth-lezer. Het systeem stelt operators in staat direct verbinding te maken met een database met meer dan 900.000 stukken gereedschap via een native IOS- of Android-toepassing. De uitgebreide informatie in het systeem omvat gereedschapsspecificaties, beheer van de gereedschapsgeschiedenis en andere functies, zoals mogelijkheden voor groepscommunicatie voor het uitwisselen van opmerkingen en projectdetails tussen meerdere deelnemers. Werkplaatspersoneel kan bovendien dezelfde RFID-technologie gebruiken om meetinstrumenten en andere werkplaatsartikelen te identificeren.
Real-time monitoring van machines helpt bij het verwezenlijken van economische duurzaamheid, omdat het daardoor mogelijk wordt materiaalbewerkingsprocessen continu te volgen. Wat betreft klanttevredenheid als element van economische duurzaamheid: monitoring biedt het productiepersoneel de mogelijkheid om een klant onmiddellijk te vertellen in welk stadium van het productieproces zijn of haar bestelling zich bevindt en wanneer deze wordt geleverd.
Voor Seco Machine Monitoring werkt Seco Tools samen met MachineMetrics, een leverancier van industriële Internet of Things (IIoT) machineplatformen. Machine Monitoring maakt Ethernet-, wifi- en mobiele communicatie mogelijk en maakt direct verbinding met de PLC's en de besturing van machinegereedschappen. Digitale en analoge I/O wordt geconfigureerd en beheerd via een webinterface. Het cloudgebaseerde systeem is gebruiksvriendelijk, volledig aanpasbaar en snel te installeren. Het systeem registreert bewerkingsgegevens en biedt productieanalyses waarmee gebruikers meer te weten kunnen komen over hun werkzaamheden en waarmee ze het gebruik en de capaciteit van hun gereedschapsmachines kunnen verbeteren. Het maakt ook interactie mogelijk met de snijgereedschap-database en ervaring van Seco, zodat gebruikers hun processen kunnen verbeteren en volledig gebruik kunnen maken van data met betrekking tot de standtijd, snelheid en voedingsoptimalisatie en als het gaat om defecte gereedschappen.

Figure 4:
HQ_ILL_Seco Tools Digital Offering.jpg
Door:
Patrick de Vos, Business Development Manager & Technical Education Manager Seco Consultancy